instructions to all persons of japanese ancestry
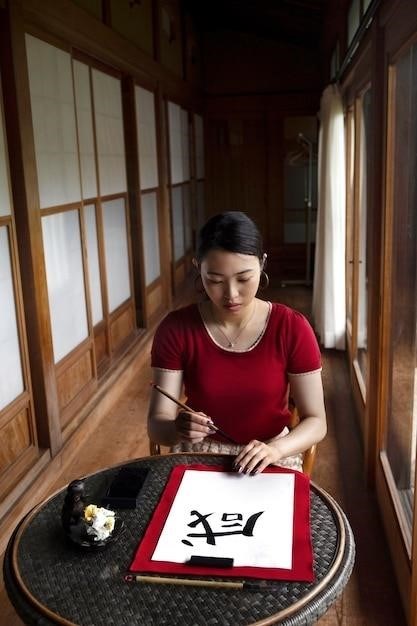
Instructions to All Persons of Japanese Ancestry⁚ A Historical Overview
The phrase “Instructions to All Persons of Japanese Ancestry” marked a dark period in American history. These instructions, issued during World War II, were a direct consequence of Executive Order 9066, which authorized the forced removal and internment of Japanese Americans. These chilling words signaled the beginning of a devastating chapter for Japanese Americans, forever etched in the annals of American history.
The Context of Executive Order 9066
Executive Order 9066, signed by President Franklin D. Roosevelt on February 19, 1942, emerged from the heightened fear and suspicion that gripped the United States following the Japanese attack on Pearl Harbor. The order authorized the military to designate certain areas as “military zones” and to exclude “any or all persons” from these areas. This broad authority paved the way for the mass displacement and incarceration of Japanese Americans, regardless of their citizenship status. The order was justified by the government as a necessary measure to protect national security, claiming that Japanese Americans posed a potential threat to the country. However, it was based on racial prejudice and fear rather than any credible evidence of espionage or sabotage.
The order itself did not explicitly mention Japanese Americans, but its application was overwhelmingly directed at them. This was due to the prevailing racist sentiment that equated Japanese Americans with the Japanese government and the widespread fear that they might be loyal to Japan. The government’s rationale was further fueled by the perception that Japanese Americans were “enemy aliens” despite the fact that many were American citizens. This perception, coupled with the war hysteria that gripped the nation, led to the implementation of a series of Civilian Exclusion Orders, which effectively forced Japanese Americans out of their homes and into internment camps.
The Infamous First Words⁚ “Instructions to All Persons of Japanese Ancestry”
The stark words “Instructions to All Persons of Japanese Ancestry” became a chilling symbol of the government’s discriminatory actions against Japanese Americans. These instructions, printed on posters and distributed throughout the West Coast, served as official pronouncements of the forced evacuation orders. They were the first tangible evidence of the government’s intent to forcibly remove Japanese Americans from their homes and communities. The starkness of the language, devoid of any pretense of compassion or fairness, reflected the prevailing atmosphere of fear and suspicion that fueled the internment policy.
The posters, often accompanied by Civilian Exclusion Orders, bore the official seal of the Western Defense Command and Fourth Army Wartime Civil Control Administration. They were posted in public places, including schools, businesses, and community centers, ensuring that Japanese Americans were fully aware of their impending fate. The posters were designed to be both informative and intimidating, leaving no room for doubt about the government’s authority and the urgency of the situation. They served as a stark reminder of the power dynamics at play, highlighting the vulnerability of Japanese Americans in the face of government decree.
The Content of the Instructions
The “Instructions to All Persons of Japanese Ancestry” detailed the steps Japanese Americans were required to take in preparation for their forced removal. These instructions were stark and impersonal, devoid of any empathy for the families and individuals they affected. They mandated the disposal of property, leaving behind homes, businesses, and cherished possessions. The instructions demanded that Japanese Americans prepare for an uncertain future, stripped of their rights and forced to abandon their lives. They were instructed to report to designated assembly centers, where they would be held before being transported to internment camps.
The instructions outlined the specific items Japanese Americans were allowed to bring with them, emphasizing a strict limit on personal belongings. This restriction further underscored the government’s intention to sever ties with their past lives. The instructions also mandated the surrender of valuable possessions, including automobiles, boats, and livestock. This requirement served to further destabilize their lives, leaving them at the mercy of the government’s authority. The instructions were a blueprint for dispossession, a calculated plan to strip Japanese Americans of their belongings and their sense of security.
The Impact of the Evacuation Orders
The evacuation orders, a direct consequence of the “Instructions to All Persons of Japanese Ancestry,” had a devastating impact on Japanese American communities. Families were forced to abruptly uproot their lives, leaving behind homes, businesses, and cherished possessions. The loss of property and livelihood was a profound blow, leaving many families in dire straits. The forced relocation also shattered the social fabric of Japanese American communities, disrupting long-standing relationships and breaking apart families. The sudden displacement caused deep psychological trauma, creating a sense of fear, uncertainty, and loss.
The evacuation orders fostered a climate of suspicion and distrust within American society. Japanese Americans, who had been loyal citizens, were now branded as enemies, their loyalty questioned solely based on their ancestry. The orders reinforced racist stereotypes and fueled anti-Japanese sentiment, contributing to a pervasive atmosphere of fear and prejudice. The evacuation orders, while seemingly aimed at protecting national security, ultimately served to exacerbate existing prejudices and undermine the fabric of American democracy. The impact of these orders resonated throughout Japanese American communities, leaving a lasting scar on their lives and their sense of belonging in America.
The Role of the Western Defense Command
The Western Defense Command, under the leadership of Lieutenant General John L. DeWitt, played a pivotal role in implementing the “Instructions to All Persons of Japanese Ancestry.” DeWitt, deeply influenced by racist fears and stereotypes, saw Japanese Americans as a potential threat to national security, despite a lack of evidence. The Western Defense Command, under DeWitt’s command, issued the Civilian Exclusion Orders, which mandated the forced evacuation of Japanese Americans from designated areas along the West Coast. These orders, often accompanied by the ominous phrase “Instructions to All Persons of Japanese Ancestry,” were the official mechanisms for carrying out the mass removal of Japanese Americans from their homes and communities.
The Western Defense Command established Civilian Control Stations, where Japanese Americans were forced to report before being transported to internment camps. The command was responsible for overseeing the logistics of the evacuation, including the transportation of individuals and their limited belongings. The Western Defense Command’s actions, driven by fear and prejudice, resulted in the unjust displacement and internment of tens of thousands of Japanese Americans, a tragic chapter in American history.
The Civilian Exclusion Orders
The Civilian Exclusion Orders, issued by the Western Defense Command under the authority of Executive Order 9066, were the legal instruments that enforced the forced removal of Japanese Americans from designated areas on the West Coast. These orders, often bearing the stark title “Instructions to All Persons of Japanese Ancestry,” were publicly posted in communities, leaving Japanese Americans with little time to prepare for their forced relocation. The orders defined specific geographic zones from which Japanese Americans were to be excluded, effectively transforming their homes and livelihoods into forbidden territory.
Each Civilian Exclusion Order contained instructions on the evacuation process, including the designated assembly points and the limited personal possessions allowed. The orders often specified a deadline for the evacuation, leaving families with little time to sell their property, businesses, or belongings. The Civilian Exclusion Orders, coupled with the pervasive fear and prejudice of the time, created a climate of anxiety and uncertainty for Japanese Americans, forcing them to abandon their homes and communities with little notice.
The Forced Relocation to Internment Camps
The Civilian Exclusion Orders, issued by the Western Defense Command, paved the way for the forced relocation of Japanese Americans to internment camps. These camps, located in remote and often harsh environments, were designed to hold Japanese Americans for the duration of the war. The conditions in these camps varied, but they were generally characterized by cramped living quarters, limited privacy, and a lack of basic amenities. Japanese Americans were forced to leave behind their homes, businesses, and possessions, enduring a significant disruption to their lives.
The internment camps were a stark contrast to the lives that Japanese Americans had built for themselves in the United States. They were subjected to constant surveillance, restrictions on their movements, and a loss of personal freedom. The internment camps were a traumatic experience for Japanese Americans, leaving lasting psychological scars on many individuals and families. The forced relocation to internment camps, a direct result of the “Instructions to All Persons of Japanese Ancestry,” represented a profound injustice, denying Japanese Americans their basic rights and freedoms during a time of national crisis.
The Legal Challenges to the Internment
The internment of Japanese Americans, though rooted in fear and prejudice, was not without legal challenges. Individuals and organizations challenged the constitutionality of Executive Order 9066 and the subsequent Civilian Exclusion Orders in court. These legal battles aimed to overturn the government’s authority to forcibly remove and detain individuals based solely on their ancestry. The Supreme Court, in the landmark case of Korematsu v. United States (1944), upheld the constitutionality of the internment program, ruling that the government’s actions were justified by military necessity.
This decision, however, was highly controversial and has been widely criticized in subsequent years. Many legal scholars and historians argue that the Supreme Court’s decision was based on racial prejudice and a flawed understanding of the threat posed by Japanese Americans. Despite the Supreme Court’s ruling, the legal challenges against the internment program continued, albeit with limited success. These challenges shed light on the legal and ethical complexities surrounding the internment program, raising questions about the balance between national security and individual rights in times of crisis.
The Legacy of the Internment
The internment of Japanese Americans during World War II left an indelible mark on American history and the lives of those affected. The legacy of this period of injustice continues to be felt today, prompting reflection on the enduring consequences of prejudice and discrimination. The internment experience, while deeply painful, also served as a catalyst for activism and advocacy. Japanese Americans, along with allies, fought for redress and recognition of the wrongs committed against them.
This struggle culminated in the passage of the Civil Liberties Act of 1988, which formally acknowledged the injustice of the internment and offered a formal apology from the United States government. The act also provided compensation to survivors of the internment. While the legacy of the internment remains a painful reminder of the dangers of prejudice and the fragility of civil liberties, it also serves as a powerful testament to the resilience and activism of those who fought for justice and remembrance. The internment serves as a critical reminder of the importance of protecting individual rights and challenging discriminatory practices in all forms;
The Importance of Remembering
The “Instructions to All Persons of Japanese Ancestry” and the subsequent internment of Japanese Americans during World War II are not mere historical events, but a stark reminder of the dangers of prejudice and the fragility of civil liberties. Remembering this period is not simply about dwelling on the past, but rather about learning from it to ensure that such injustices are never repeated. By remembering, we acknowledge the pain and suffering inflicted on innocent individuals and families, and we honor the resilience of those who endured such hardship.
Remembering also serves as a crucial tool for promoting understanding and empathy. By learning about the internment, we gain insights into the complexities of race, prejudice, and wartime hysteria. This understanding can help us to identify and challenge similar forms of discrimination in our own time. Remembering the internment is an act of vigilance, a commitment to safeguarding our democratic values and ensuring that history does not repeat itself. By keeping the memory of the internment alive, we can work to build a more just and equitable society for all.