rain bird sprinkler controller manual
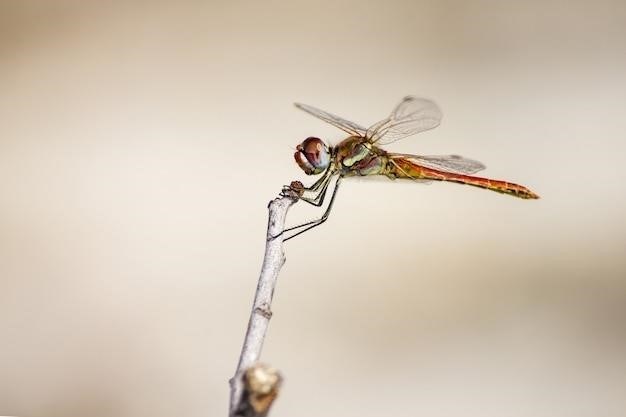
Rain Bird Sprinkler Controller Manuals⁚ A Comprehensive Guide
This comprehensive guide provides a detailed overview of Rain Bird sprinkler controller manuals‚ covering various models‚ features‚ and support resources. Whether you’re a homeowner‚ landscaper‚ or irrigation professional‚ this guide will equip you with the knowledge to effectively use and maintain your Rain Bird system.
Introduction
Rain Bird‚ a renowned name in the irrigation industry‚ offers a wide range of sprinkler controllers designed to automate and optimize your watering system. These controllers provide precise control over watering schedules‚ ensuring efficient water usage and healthy lawn and garden growth. Understanding the intricacies of your Rain Bird sprinkler controller is crucial for maximizing its benefits and ensuring optimal performance.
This guide serves as a valuable resource for navigating the world of Rain Bird sprinkler controller manuals. It delves into the diverse types of controllers available‚ highlighting their unique features and functionalities. Whether you’re seeking information on the ESP-TM2‚ ESP-ME3‚ TBOS-II‚ or other models‚ this guide provides comprehensive insights into their operation‚ programming‚ and troubleshooting.
We also explore the Rain Bird Support Center‚ a valuable hub for accessing manuals‚ literature‚ and video tutorials on both current and discontinued products. This comprehensive resource empowers you to find answers to your questions and gain a deeper understanding of your controller. Furthermore‚ we address common troubleshooting issues and maintenance tips‚ ensuring the longevity and efficiency of your Rain Bird system.
By delving into this guide‚ you’ll gain a thorough grasp of Rain Bird sprinkler controller manuals‚ empowering you to navigate the complexities of your system and maximize its benefits.
Types of Rain Bird Controllers
Rain Bird offers a diverse range of sprinkler controllers catering to various needs and applications. Each controller boasts unique features and functionalities‚ allowing you to select the best option for your specific landscape and irrigation requirements. Here’s a glimpse into some popular types⁚
- ESP-TM2 Controller⁚ The ESP-TM2 is a versatile controller known for its user-friendly interface and reliable performance. It offers manual operation‚ automatic scheduling‚ and integration with weather sensors. This controller is ideal for residential and small commercial applications.
- ESP-ME3 Modular Irrigation Controller⁚ The ESP-ME3 is a modular controller designed for larger‚ more complex irrigation systems. Its modular design allows for easy expansion and customization‚ accommodating various valve configurations and system requirements. This controller is well-suited for commercial landscapes and large-scale irrigation projects.
- Rain Bird TBOS-II Battery-Operated Controller⁚ The TBOS-II is a battery-powered controller offering flexibility and portability. This controller is ideal for remote irrigation systems or areas lacking a power source. It features a redesigned handheld transmitter for convenient operation.
- Rain Bird Two-Wire Decoder Systems⁚ Two-Wire Decoder Systems are designed for cost-effective control of multiple valves over long distances. These systems utilize a two-wire communication protocol‚ reducing the need for extensive wiring and simplifying installation. They are commonly used in large commercial and agricultural applications.
- Rain Bird Simple To Set Timer⁚ As the name suggests‚ the Simple To Set Timer is designed for ease of use. This controller offers straightforward programming and intuitive operation‚ making it an excellent choice for homeowners seeking a simple and reliable solution.
Understanding the specific features and capabilities of each controller type is crucial for selecting the most suitable option for your irrigation needs. Consulting the relevant Rain Bird manuals provides detailed information on each controller’s operation and programming.
ESP-TM2 Controller Manual
The Rain Bird ESP-TM2 controller is a popular choice for homeowners and landscape professionals seeking a reliable and user-friendly irrigation solution. The ESP-TM2 manual provides comprehensive instructions for installation‚ programming‚ and operation of the controller. It covers various aspects‚ including⁚
- Installation Guide⁚ The manual outlines the proper installation procedures for the ESP-TM2‚ ensuring correct wiring and connections to the sprinkler system. It provides diagrams and step-by-step instructions for a seamless installation process.
- Programming Instructions⁚ The manual guides users through the programming process‚ explaining how to set watering schedules‚ adjust run times‚ and configure various settings. It provides clear explanations and examples for easy comprehension.
- Manual Operation⁚ The ESP-TM2 manual covers the functionality of manual operation‚ allowing users to manually turn on and off specific zones as needed. It explains how to select zones‚ adjust run times‚ and utilize manual control features.
- Troubleshooting Guide⁚ The manual includes a troubleshooting guide to assist users in resolving common issues that may arise with the ESP-TM2 controller. It provides solutions for problems like malfunctioning valves‚ incorrect programming‚ and power supply issues.
- Advanced Features⁚ The manual details advanced features of the ESP-TM2‚ such as integration with weather sensors‚ remote control capabilities‚ and advanced scheduling options. It explains how to utilize these features to optimize irrigation efficiency and water conservation.
The ESP-TM2 manual is an invaluable resource for understanding and effectively operating this controller. By carefully reviewing the manual‚ users can ensure proper installation‚ programming‚ and troubleshooting of their Rain Bird ESP-TM2 sprinkler system.
ESP-ME3 Modular Irrigation Controller
The Rain Bird ESP-ME3 modular irrigation controller is a versatile and expandable system designed to meet the needs of residential and commercial applications. The ESP-ME3 manual provides detailed instructions for installation‚ programming‚ and operation‚ covering a wide range of features and functionalities.
- Modular Design⁚ The manual emphasizes the modular design of the ESP-ME3‚ allowing users to customize the controller to their specific irrigation requirements. It explains how to add or remove modules‚ such as valve stations‚ rain sensors‚ and remote control units‚ to create a tailored system.
- Programming Flexibility⁚ The ESP-ME3 manual outlines the flexibility of programming options‚ enabling users to create customized watering schedules for different zones based on factors like plant type‚ soil conditions‚ and weather patterns. It provides step-by-step instructions for setting watering days‚ times‚ and durations.
- Advanced Control Features⁚ The manual highlights the advanced control features of the ESP-ME3‚ including integration with weather sensors‚ remote control capabilities‚ and automatic adjustments for optimal irrigation efficiency. It explains how to utilize these features to conserve water and reduce operating costs.
- Troubleshooting and Maintenance⁚ The ESP-ME3 manual includes a comprehensive troubleshooting guide to assist users in resolving common issues. It provides solutions for problems like malfunctioning valves‚ incorrect programming‚ and power supply issues. It also outlines recommended maintenance procedures to ensure the longevity and optimal performance of the controller.
- Connectivity and Compatibility⁚ The ESP-ME3 manual explores the connectivity and compatibility options of the controller‚ including its ability to integrate with Rain Bird’s remote management platforms. It explains how to connect the controller to Wi-Fi or cellular networks for remote access and control.
The ESP-ME3 manual is an essential resource for understanding and effectively operating this modular irrigation controller. By carefully reviewing the manual‚ users can maximize the benefits of the ESP-ME3‚ ensuring a reliable and efficient irrigation system.
Rain Bird TBOS-II Battery-Operated Controller
The Rain Bird TBOS-II is a battery-operated controller designed for remote irrigation applications where traditional wired controllers are not feasible. The manual for the TBOS-II provides comprehensive instructions for installation‚ programming‚ and operation‚ ensuring users can effectively manage their irrigation systems in remote locations.
- Wireless Operation⁚ The TBOS-II manual emphasizes the controller’s wireless capabilities‚ allowing users to control their irrigation system from a distance using a handheld transmitter. It explains how to pair the transmitter with the controller and program watering schedules for different zones.
- Battery Power⁚ The manual details the controller’s battery-powered design‚ providing information about battery life‚ charging procedures‚ and low-battery indicators. It also outlines the controller’s power-saving features‚ ensuring optimal battery efficiency.
- Zone Programming⁚ The TBOS-II manual provides step-by-step instructions for programming watering schedules for each zone. Users can set watering days‚ times‚ and durations‚ as well as adjust watering intervals based on plant needs and weather conditions.
- Advanced Features⁚ The manual highlights the TBOS-II’s advanced features‚ including rain sensors‚ manual override options‚ and the ability to store multiple watering programs. It explains how to utilize these features for efficient and customized irrigation management.
- Troubleshooting and Maintenance⁚ The TBOS-II manual includes a troubleshooting guide to help users resolve common issues‚ such as battery problems‚ communication errors‚ and valve malfunctions. It also outlines recommended maintenance procedures to ensure the longevity and optimal performance of the controller.
The TBOS-II manual is a valuable resource for users who need a reliable and convenient way to control their irrigation systems in remote settings. By following the instructions in the manual‚ users can maximize the benefits of the TBOS-II‚ ensuring efficient and effective irrigation management for their remote properties.
Rain Bird Two-Wire Decoder Systems
Rain Bird Two-Wire Decoder systems offer an efficient and cost-effective solution for controlling multiple valves within a large irrigation system using just two wires. The manuals for these systems provide detailed instructions for installation‚ programming‚ and troubleshooting‚ ensuring seamless operation and optimal performance.
- System Overview⁚ The manuals provide a comprehensive overview of the two-wire decoder system‚ explaining its components‚ including the decoder unit‚ control panel‚ and valve actuators. It outlines the principles of operation‚ illustrating how signals are transmitted over the two wires to control multiple valves.
- Installation Guide⁚ Detailed instructions for installing the two-wire decoder system are included‚ outlining the proper wiring connections‚ placement of the decoder unit‚ and installation of valve actuators. The manuals emphasize safety precautions and wiring standards to ensure a secure and functional system.
- Programming and Operation⁚ The manuals guide users through the process of programming the decoder system‚ explaining how to set watering schedules‚ adjust watering durations‚ and configure different zones. It details how to use the control panel to manage the system and monitor its operation.
- Troubleshooting and Maintenance⁚ The manuals include a troubleshooting section to help users diagnose and resolve common problems‚ such as communication errors‚ valve malfunctions‚ and power issues. It also outlines recommended maintenance procedures‚ including regular checks of wiring connections and valve operation‚ to ensure system longevity and optimal performance.
- Compatibility and Applications⁚ The manuals highlight the compatibility of the two-wire decoder systems with various Rain Bird controllers and valve actuators‚ providing information on compatible models and specifications. It also outlines the system’s versatility‚ indicating its suitability for diverse irrigation applications‚ including residential‚ commercial‚ and agricultural settings.
By carefully following the instructions in the manuals for Rain Bird Two-Wire Decoder systems‚ users can ensure proper installation‚ effective programming‚ and efficient operation‚ maximizing the benefits of this cost-effective and reliable irrigation control solution.
Rain Bird Simple To Set Timer Manual
The Rain Bird Simple To Set Timer manual offers a user-friendly guide to programming and operating this straightforward sprinkler controller. It provides clear and concise instructions‚ making it easy for homeowners to set up and manage their watering schedules‚ ensuring their lawns and gardens receive the appropriate amount of moisture.
- Introduction and Features⁚ The manual begins by introducing the Simple To Set Timer‚ outlining its key features and benefits‚ such as its ease of use‚ intuitive interface‚ and reliable performance. It highlights the timer’s ability to create customized watering schedules for different zones‚ providing flexibility and control over irrigation.
- Installation and Wiring⁚ The manual provides step-by-step instructions for installing the Simple To Set Timer‚ including proper wiring connections‚ valve configuration‚ and placement of the timer. It emphasizes safety precautions and wiring standards to ensure a secure and functional installation.
- Programming Guide⁚ The manual offers a comprehensive guide to programming the timer‚ explaining how to set watering days‚ durations‚ and start times for each zone. It uses clear diagrams and illustrations to visually demonstrate the programming process‚ making it easy to understand even for novice users.
- Manual Operation and Troubleshooting⁚ The manual includes instructions for manual operation‚ allowing users to manually activate or deactivate specific zones as needed. It also provides a troubleshooting section‚ addressing common problems that users might encounter and offering solutions to restore proper operation.
- Maintenance and Warranty Information⁚ The manual outlines recommended maintenance procedures for the Simple To Set Timer‚ including cleaning the timer‚ checking valve operation‚ and ensuring proper water pressure. It also provides information on the warranty period and contact details for customer support.
The Rain Bird Simple To Set Timer manual empowers users to confidently set up and manage their irrigation system‚ ensuring their landscapes thrive with the right amount of water‚ all while providing peace of mind with its user-friendly design and comprehensive instructions.
Rain Bird Support Center
The Rain Bird Support Center serves as a valuable resource for users seeking assistance with their sprinkler controller manuals‚ technical information‚ and product support. This comprehensive online platform offers a wide range of resources to ensure users have access to the information they need to operate and maintain their Rain Bird systems effectively.
- Manuals and Literature⁚ The Support Center houses a comprehensive library of manuals‚ literature‚ and guides for current and discontinued Rain Bird products. Users can easily access and download PDF versions of manuals‚ installation guides‚ troubleshooting tips‚ and other relevant documents for their specific controller model.
- Videos and Tutorials⁚ The Support Center provides a collection of instructional videos and tutorials that guide users through various aspects of their Rain Bird systems‚ from installation and programming to troubleshooting and maintenance. These visual aids offer a clear and concise way to understand complex concepts and solve common issues.
- Product Information and FAQs⁚ The Support Center provides detailed information on all Rain Bird products‚ including specifications‚ features‚ and compatibility details. It also includes a frequently asked questions (FAQs) section‚ addressing common user inquiries and providing quick answers to frequently encountered problems.
- Contact Support⁚ The Support Center offers multiple ways for users to contact Rain Bird’s dedicated customer support team. Users can submit inquiries through an online form‚ call a toll-free number‚ or engage in live chat sessions with support representatives. This ensures prompt assistance for any technical issues or questions that may arise.
By providing readily available resources‚ comprehensive information‚ and direct access to support‚ the Rain Bird Support Center empowers users to confidently operate and maintain their sprinkler systems‚ ensuring optimal performance and longevity.